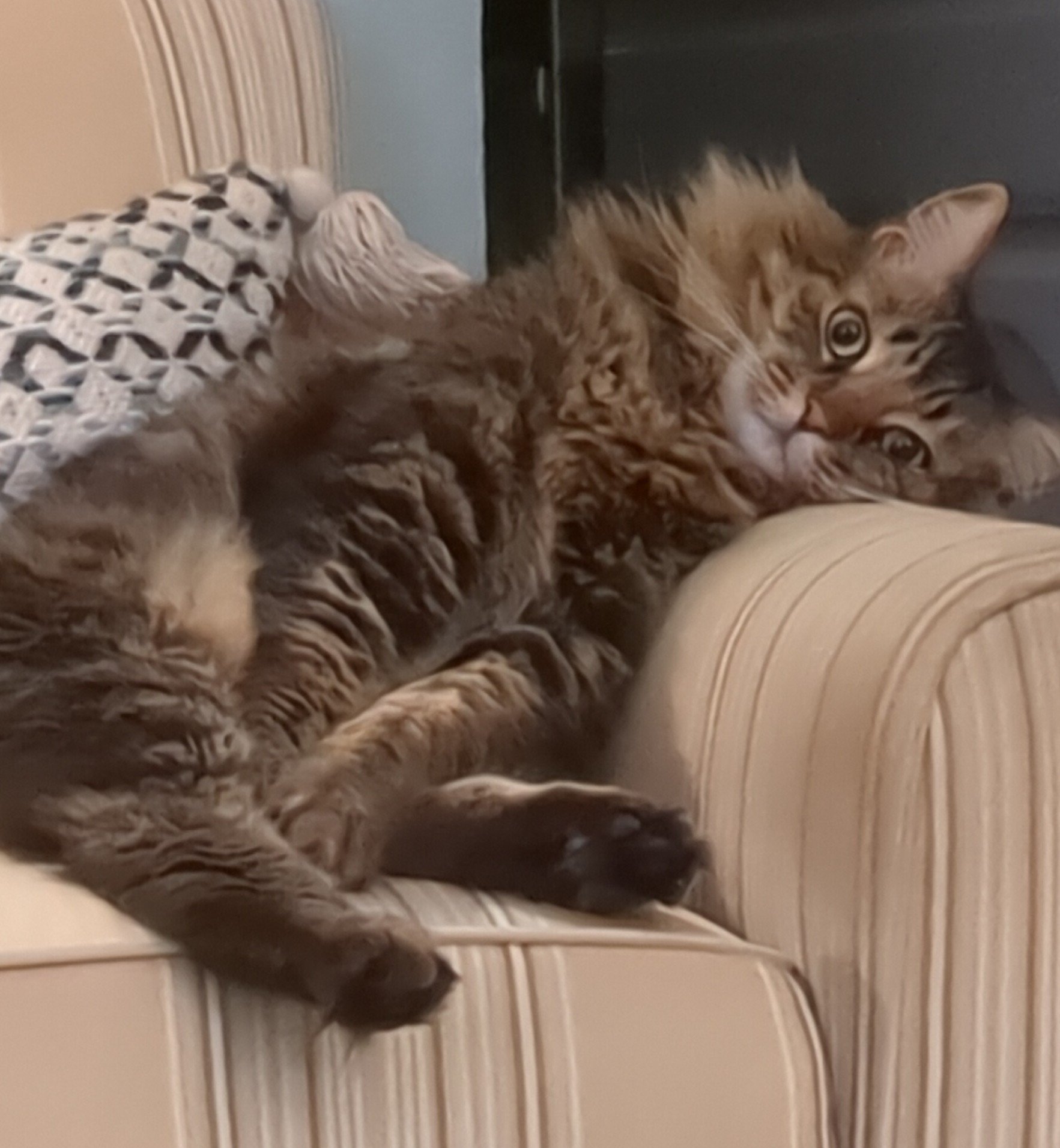
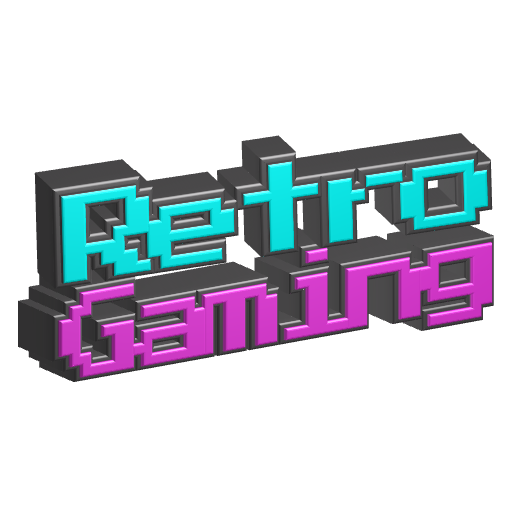
I don’t trust AliEx any more after I took the loss of 3 orders for ~$60 in 2020. When I called, they hung up on me at random every time. After the 3rd try I washed my hands and walked away. Stealing from me once is on them, twice would be my own fault. Prior to that experience I spent a few thousand dollars on the platform for odds and ends.
I expect something like this to be an emulator and nowhere near the quality of a real Nintendo product, but I could be wrong. I would buy used or a homebrew project that is well documented and might cost a little more.
deleted by creator