
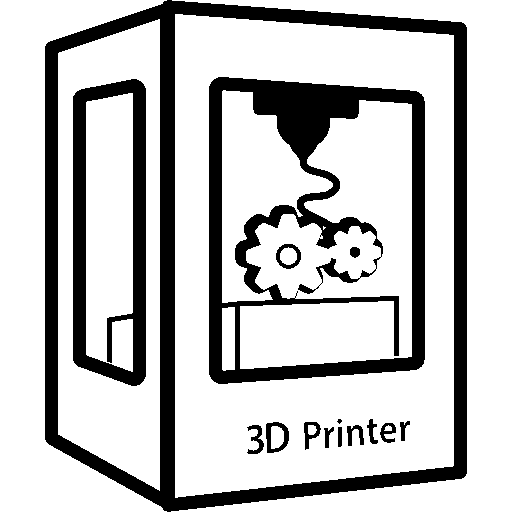
Excellent, reader cases always seem to cost way more than they should, espeically with how fragile they are.
Although, you should know you’re supposed to move over to another room to pretend your workspace is cleaner than workspaces ever are, LOL. Then, what are we rocking for the keyboard?
You could also probably use Inkscape to get DXF files for both sides of the coin, making sure the size is right and that the path accommodates the width of your letters/strokes. Then, hypothetically, you should be able to import the files as drafts and then convert them to sketches with the press of a button (in reality, this crashes FreeCAD for me lately, but it could be a quirk of my setup). If you’ve already modeled the coin itself and use the new sketches to pocket into the existing solid, IIRC it should work okay. FreeCAD would not extrude a non-contiguous sketch into multiple solids, but I think it’s fine as long as the end result is still a single body.