
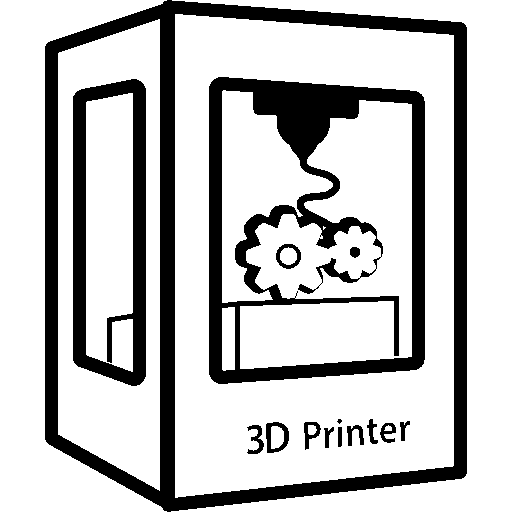
Nice! This is really impressive for a first prototype print. I’ve been printing for over a year, designing small brackets and such for maybe 6 months, and most of my designs are just one solid piece. Something with moving parts is awesome!
Can we ask what the project this is for is, or for a link to this model?
Fantastic! My first thought was either a miniature display table or maybe a small parts case-and-table combo.