
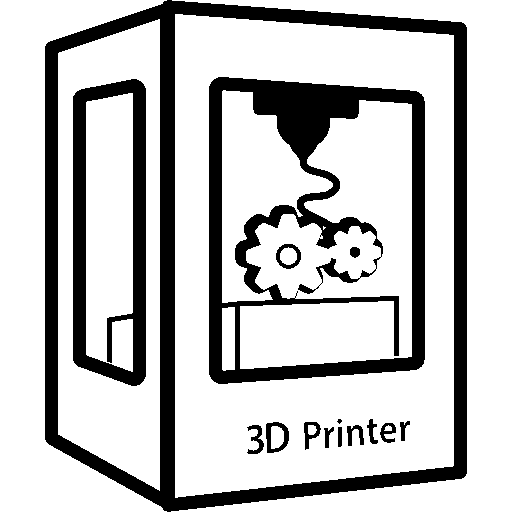
Fingers crossed. There’s hats you can get to power the pi off of printer’s 24v supply, considering doing it on my klippered mk3s and switch that over to using a SBC instead of the laptop.
If you can swing it, definitely worth printing a spare set for the stealthburner + cw2, just in case you crack anything during assembly.
Totally get you, I swapped my prusa’s hotend for a stealthburner as well, they’re super nice to service, especially with the 2 part PCB, but having the entire assembly mounted from the front is fantastic.
Stealthburner ended up fixing your clog issues entirely?