
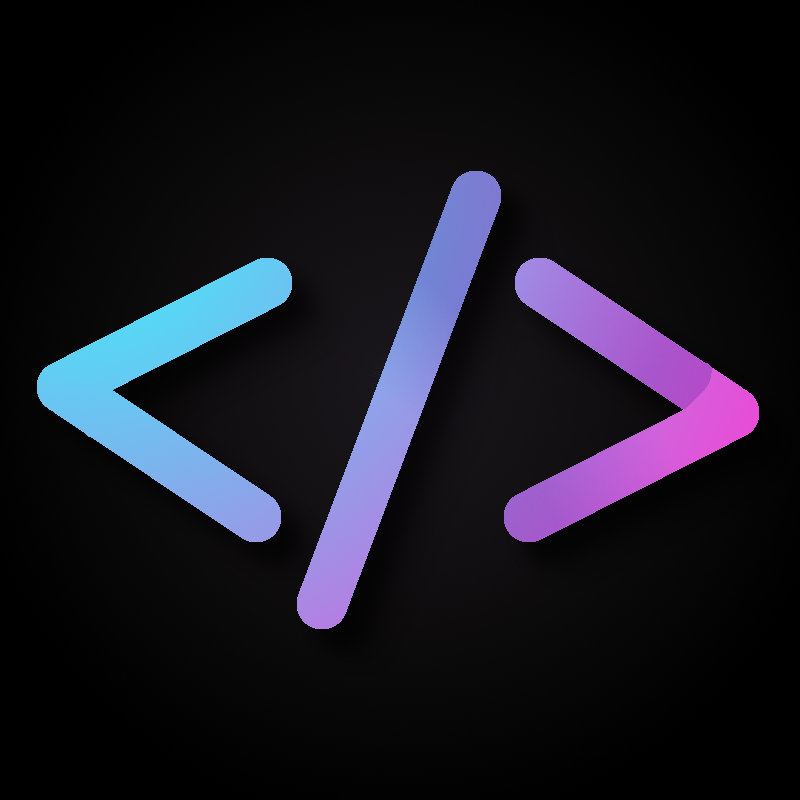
My favorite is “and there was some kind of error message.” There was? What did it say? Did it occur to you that an error message might help someone trying to diagnose your error?
My favorite is “and there was some kind of error message.” There was? What did it say? Did it occur to you that an error message might help someone trying to diagnose your error?
It looks to me like they did it this way so that it could have natural-language names in many languages. So, the function Z10096 is called “is palindrome” in English, but if you’re coding in Japanese you can call it “回文の判定”. I don’t think the idea is for people to refer primarily to the alphanumeric soup version; I think that’s just the unique identifier for the database.
It does look like it’s leading to some issues, though. E.g., someone added a test for the “is palindrome” function which uses a somewhat common example: “Straw? No, too stupid. I put soot on warts.” Now, a human would probably say that this is a palindrome, because it’s got the same letters forwards and backwards, but most of the implementations disagree, because they consider the spaces, capitalization, and punctuation to be part of the string; that is, they test whether the input string and its reverse are equal. So someone (possibly the same person) has added a second python implementation which ignores spaces, capitalization, and punctuation, and mentions that in its name on the page.
Fundamentally this function is solving a different problem than the others (as demonstrated by the differing results on the relevant test), so should it get its own number and page? should there be a “palindrome disambiguation” page? This seems like something the site will have to figure out how to handle.
Turbo Pascal was the first language in which I had serious classes (I had tutoring in Applesoft Basic earlier on, but that language has a lot of limitations), and I used it for years afterwards. You could write auxiliary functions in Turbo Assembler and link them in; I used that to write a library that allowed access to the 320x200 256-color VGA mode (the built-in graphics only did EGA and were super slow), and other libraries for mouse and joystick control. I tried to control the soundblaster for FM synthesis, but it was too complicated for me to figure out how to do anything useful without better access to documentation (this was before the world wide web). The experience also taught me a lot about assembly language basics, function calling conventions for C and Pascal, stack manipulation, and so forth, which gave me a huge head start in my compilers courses at university.
On the whole I would still recommend C over Pascal as an early language–it gives you much better insight into memory layout and so forth, where Pascal kind of obfuscates such things, and C just generally kind of acts like both Pascal and Assembler rolled together. But Turbo Pascal definitely gave me a good foundation.
Oh, I literally misread it as OpenSCAD. Laughing at my stupid brain right now.
I’d say it’s more like Premiere vs ffmpeg.
It really sounds like you’re describing Make (or LLVM). Is there something you need it to do that those can’t handle?
The only real objection I have to this as a term is that it’s too easy to confuse with “rubber ducking”: https://en.m.wikipedia.org/wiki/Rubber_duck_debugging
I do a lot of this stuff with the HP48 Units menu (albeit at this point via an emulator on my phone).
Shaders are terrific fun. I highly recommend ShaderToy if you want to experiment with them; it makes the loop between changing the code and seeing the effect very tight. I also recommend the YouTube channel “Art of Code” for good examples, well-explained.
It also doesn’t with with PLA and ABS. Same issue, they won’t stick together well.
And when you say “laser or printer” here, are you referring to a 2d printer, or a 3d printer?
The questions are because, fundamentally, a wireframe image like the one you linked is just a different way of rendering the same file. So if what you want is literally an image like this, then there are tools to do that, which will depend a bit on what operating system you’re using. Blender, as mentioned in another comment, is one such option.
If, on the other hand, what you want is a 3d printable structure that resembles a wireframe rendering of the object, that’s a more complicated task. The STL file just lists the triangles that make up the surface of the object; in order to make a solid structure that resembles this, you’d need to create a solid (e.g. a cylinder, maybe with balls at the ends) for every edge in the file (3n / 2 edges for n triangles, since every edge in a properly printable [“manifold”] STL is shared by two triangles) and then takes a boolean union of all of them. I don’t think a tool to do this exists currently, as it’s a rather specialized need, but it wouldn’t be too hard to throw together a python script that could take an STL file and generate an OpenSCAD script that you could then render with OpenSCAD to get the STL.
So, one thing to consider is whether you could have remnants of a previous filament getting stuck in your hotend and carbonizing and causing partial clogs. That depends a bit on what you were running just before running this filament. If this is the issue, a cleaning filament can help. Another possibility is that your nozzle isn’t tight against the heatbreak, in which case plastic can accumulate there and cause issues. The only way to fix that is to disassemble the hotend and put it back together correctly–this usually involves tightening the nozzle when it’s hot, but check the details for your specific printer.
But yeah, it could also just be bad filament. That’s probably the easiest thing to fix, anyway.
Sure. You can always include both as well. Folks who don’t have CAD software may not be able to use the STEP files.
Lots of people post STLs because you can feed them directly to the slicer for printing. But it only represents the surface mesh of an object, and only as polygons. A STEP file basically captures how the part is designed in CAD, so it’s much better if you need to modify the part. It also gives you the original form of things like curves, where the STL would be quantized into a fixed number of polygons.
It mostly avoids them, but it doesn’t necessarily do that on the first layer, and it does a big travel at the end to park the print head. You could probably get something to work if you wrote it with the FullControl Gcode Designer.
Travel moves wouldn’t work, because the wire core has to be continuous.
I think the best bet is to design a model with a cavity that the wire can snap into, and add the EL wire after the print is finished.
Oh, that’s a thought, I’m not sure how the strain gauges factor in.
I can’t find very good images of the bed mechanism in the machine, but it looks to me like there’s a separate piece for the machine that mounts the nut for the leadscrew to the bed. The easiest way to make it more adjustable might be to design and print a replacement for this part that allows you to use a screw to offset this connection slightly. You could probably get away with just making the front two adjustable and leaving the back one fixed.
Or it won’t happen when you’re watching, because then they’re thinking about what they’re doing and they don’t make the same unconscious mistake they did that brought up the error message. Then they get mad that “it never happens when you’re around. Why do you have to see the problem anyway? I described it to you.”