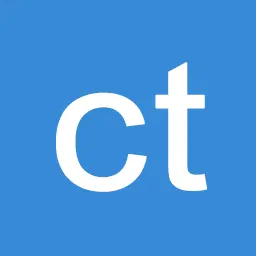
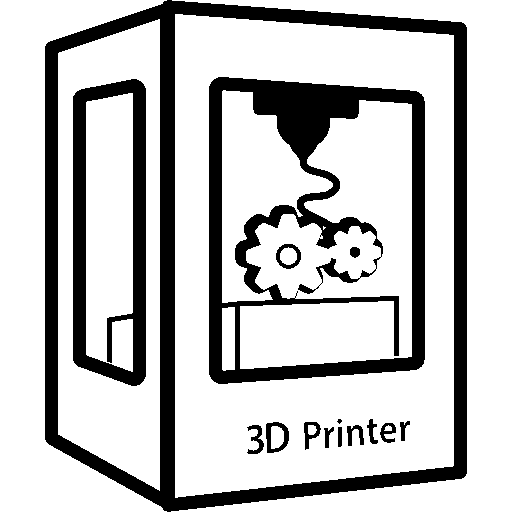
A lot of people here commented “I do X and it works for me”, but I do not think that is good advice. While it might work fine for that person, there are too many variables that are ignored. Ambient humidity, filament type, printer model, slicer settings, model geometry/details - all of this has an impact on the final print quality.
A more controlled environment removes variables and therefor makes the print result more predictable. Drying filament and storing it properly takes a bit of effort, but it is easy step towards better results.
You don’t even need a dedicated dryer, just use your printers headbed, put 1-3 spools on it and a cardboard box with a few vent holes on top. Set the temperature according to the filament and let it run for 8 hours. Afterwards put the spools into a sealed container (4L cereal box works great), add some silica gel and your done. When it cools back down the relative humidity drops below 10% RH, which is so low that most hygrometers wont even measure it.
I’m casually printing PETG at 260°C, over 20mm³/s (about 300mm/s) and archive reproducible near perfect results with next to no stringing. With bare PLA drying may not matter, I’ve too little experience to give a definitive answer. If you have any composite filament (wood, carbon, sparkle, etc) you definitely should dry it anyway, because you do not know how much the filler changes the properties.
Oh and finally: I place new spools in containers with dry air (a tiny bit of silica gel in them) and measure the equalized humidity after a few days. Most spools were delivered with a humidity of 15-20% RH
What filament do you want to use? Well tuned PLA might be able to bridge that far, no chance with PETG. What is your maximum acceptable sag?
It seems like the bridge lines do not attach to anything at the very end on the layer below. In Orca Slicer you need to enable “Ensure vertical thickness” to enforce that. I’d also rotate the bridge direction by 90°, this cuts down the length of the longest bridges by half. Bridge line spacing looks good to me. Make sure that the layer on top of the bridge is printed slowly and does not start in the middle, otherwise it will be pushed back and forth.
If it is just a mock-up, consider partially filling the interior or enabling “make overhangs printable”. Both will alter geometry, but so will excessive sagging.