
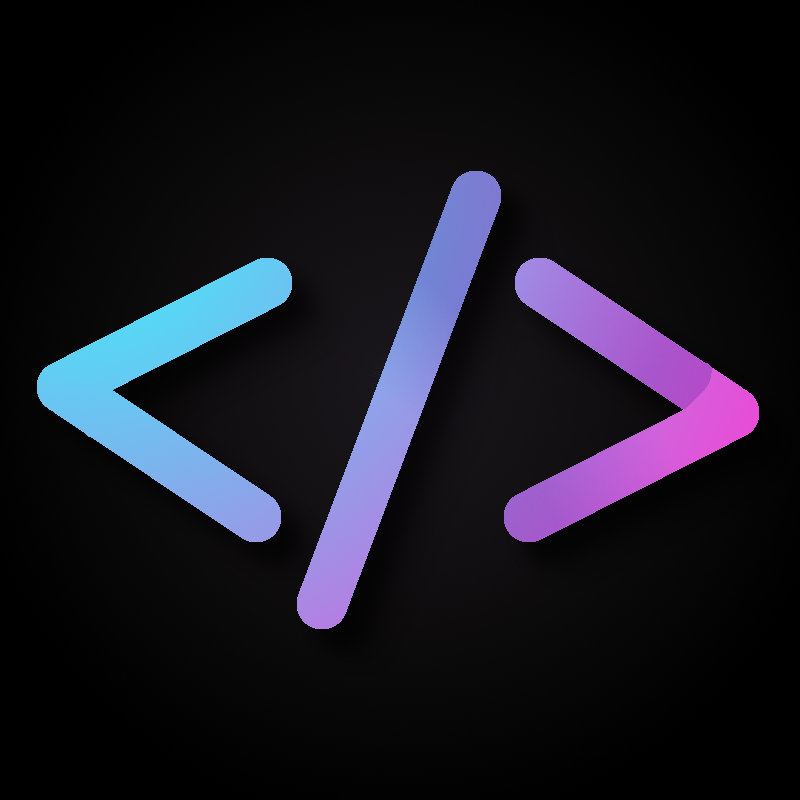
That is what I’m saying, that SDK covers more than just normal users.
That is what I’m saying, that SDK covers more than just normal users.
I mean sure but that’s a lot of words to say “I didn’t read the directions and no one caught it in a merge request review because no one else read the directions either.”
Their documentation and examples are pretty easy to read and the site parameter is explained in the getting started guide and even linked from the readme for the JavaScript sdk, and in lots of sample configurations so I’m not sure how this made it into a release and then no one noticed the missing metrics for eleven days, sounds like lots of issues in that shop.
The behavior of the sdk isn’t great but the proposed solution wouldn’t work because you can use custom endpoints for all of the components using endpoints on domains you own anyway.
Alright I’m not sure if this is the right place to ask either but if I were to guess it is s01e6 that they are referring to, I had forgotten about that show! It is really a great show from what I remember, especially that episode. Definitely worth a watch if you have not, I should watch it again.
Yep definitely agree with all of this here, my friends and I have been saying the same things about Prusa too, they need to innovate or drop their prices in 2024.
I am also a big oss supporter but the user experience of the Bambu ecosystem is really great, lately it has basically become the same argument as iPhone vs Android.
To sum it up, I usually tell people that while both work, if your interest in the hobby is in the things that come off the printer then get a Bambu, if your interest is in tinkering and optimizing the printer then get a Prusa or something.
I have a mk3s that is modded and an X1C and I always reach for the X1 because prints basically always work in any material without changing settings beyond infill/strength etc, I don’t even calibrate anything on it anymore, their auto calibrate function is extremely good and I have used it with PLA,PETG,ASA,ABS, PA/Nylon, PC, PLA/PETG/PA-CF, PLA+wood, and even TPU. The Prusa does well but it is definitely more finicky but I’m definitely a core-xy convert now so my next printer will be a core-xy because the accuracy is so much better for tall and square objects especially.
So I am definitely not an electrician by any means but I noticed on their site the ZEN05 says “Do not install the device in a place with direct sun exposure, high temperature, or humidity.” which seems pretty silly to me for something that two lines above says it is outdoor rated hah. I bet that is why they said not to use it though, heat+melting ice will generate humidity or something. I wouldn’t be placing the device next to the heating pad if it was me anyway so I would think it would work, your logic seems sound to me, I probably wouldn’t even have asked zooz now that I think about it.
That said, I’m going to need to hear more about these heating mats, I have some sidewalks that I don’t enjoy shoveling hah.
ETA: forgot to include, I use the GE version of that ZEN05 outside (since 2019) plugged into a GFCI outlet and it works fine, it definitely has very direct sun and gets all weather too.
OP, this is the way. I use the Sonoff zigbee dongle with zigbee2mqtt on a spare pi located centrally in my house and it works great, home assistant is down in the basement. I have had nothing but issues with battery powered zwave devices of many brands and all of my light switches are zwave and they work fine so it definitely wasn’t a range problem. I will probably slowly replace those with zigbee switches as they die because the zigbee mesh has just been so much more reliable.
Do make sure to throw a few mains powered zigbee devices on your mesh to act as routers once you get more than a few devices on the mesh, it also helps with range and response times.
I have never tried it but I am real curious for low speed things like that, I think it would come down to your printer being able to print something small enough. There are a bunch of print in place bearing designs on printables that I have run across too.
I usually use 608 bearings for that kind of thing because they are really cheap on Amazon as well since those are used in roller skates and skateboards and stuff. I am definitely curious though so you should reply if you try it out :D
Yeah that is similar to what I was thinking but 4 individual sets of rollers, one for each spool. This version would be annoying in a drybox because all of the filament spools will probably spin at the same time which will make them all unspool since you will probably have them fed into 4 couplers and not clipped like on a shelf. Might work though if you don’t plan on having one output for each box and switching the “active” spool but I try to not open my dry boxes in general to keep air moisture out.
I mean if it’s working then it’s probably fine, two tubes would be interesting, I would think that would be a hassle when you have to take it in and out to change the filament. I ended up switching to using rollers on the bottom because of that anyway. I was going to try that one I linked before but I started designing my own similar one that used 1/2” EMT and bearings as rollers, I should finish that hah.
You can use PVC, if you are planning to hang it vs using the PVC as rollers then you will need larger diameter and maybe schedule 80 or it will be two flexible and sag in the middle. When I tested it I could get about 4 rolls on a 1.5” diameter piece of PVC before it started sagging. You might want to look at using EMT conduit for that, that’s what I switched to using for shelves and it works better.
Does not have to be spaced but any friction can cause drag if you are printing from the drybox which can be a problem depending on your extruder and how much drag.
Fitting thread size doesn’t matter if you are just screwing them into the drybox, what matters is the tube size it supports, M4 or M10 would only matter if you were using them on something that was pre threaded. For what it’s worth I just standardized on the PC4-M10 ones because there was a huge pack on Amazon that was cheap hah.
I use these bins and I want to try this roller print (not my model) because it looks real simple, I don’t print from the boxes very often though so I haven’t bothered.
Hope that helps!
Yeah! Once I learned a few basics and how to think in parametric it didn’t take long until I could make things that were in my mind which felt like a huge accomplishment. It still blows my min every time I think of something and then am holding it in my hand an hour later, it’s definitely worth the time.
I ended up just paying for the basic fusion license because I quickly had more than 10 ideas I wanted to work on hah. I know it’s expensive but compared to the other options it is by far the most reasonable, especially if you ever want to sell anything you design. I also felt like I would spend that much on a physical tool to do a project if I needed it so :shrug: but the free version is definitely workable.
The other thing that frustrated me was manipulating the view and to solve that I finally broke down and bought a space mouse which is an absolute game changer, I shouldn’t have waited so long and I will never go back haha. I found a deal on one on eBay but there are also a few DIY printable projects like this one which look awesome and I might build anyway.
ETA: The space mouse works in many applications, it even works in Bambu/Orca slicer!
No you can only have 10 read/write models at the same time but as far as I found you can store as many read-only models as you want and you can toggle them back and forth. Also, you also can store the files locally, or at least export them to a local fusion file.
Okay we sound similar so I want to make sure you found this playlist about fusion 360.
I recently had the time to sit down and spend time learning fusion after a delete failed attempts previously and the biggest lightbulb moment I had was really getting in the mindset of how parametric cad works. I guess I had assumed it was a buzzword coming from IT but no, it’s like the difference between building infrastructure manually and building infrastructure with something like Terraform.
The other thing that was a big lightbulb for me is learning how to use the history in fusion, the first time I went back in the timeline and changed a dimension and it recalculated everything I about fell out of my chair.
Anyway, I hope that is helpful, I can try to answer questions but I am certainly no expert in fusion hah. that playlist above is what I used to get going, definitely haven’t watched all of it but the first few were really helpful.
Oh also, on shape and others are also parametric style cad so that is probably why they all seemed similarly frustrating.
My guess is that is a slicer error because it couldn’t make the shape with a combination of the tooth size on the gear and wall thickness settings. Does it look right in the slicer after it is sliced on the first layer?
I want to add a second to everything this person said, I have both a Mk3s that has some upgrades and an X1C and the difference in speed and quality is astounding. They are not kidding either, the quality out of the box is excellent. I basically only change strength related parameters anymore, the automatic flow calibration is incredible. The recent addition of the ability to skip failed parts mid print from my phone is awesome as well. I have also printed the same part with the same layer height and filament and the X1 is almost 3x as fast in “standard” preset.
Also for what it’s worth, I am probably going to replace my Mk3 with the A1 in the next few months as well.
You definitely can’t, they don’t really adhere to each other at all. Like even to the extent that you can actually use PETG as easily removable support material for PLA.
I definitely recommend Fully Kiosk Browser, it’s easily worth the 10$ license even if you don’t need the features. The integration into Home Assistant is great, you can do all kinds of things really easily to the app through HA like loading URLs and controlling the screen on and off, the integration is really superb.
ETA: I forgot, it also has a webui to manage it remotely. Also, I’m pretty sure it’s free still, I just mean it’s that good of an app that it’s worth whatever their license costs (I bought it a while ago).
For what it’s worth, I would bet finishing an FDM print with paint will be more annoying due to the layer lines before the scale would get in the way with a modern 3d printer as FDM does not produce a smooth surface finish like an injection molded part without further post processing like vapor smoothing which would also eat the details. I don’t have a resin printer though so I could be totally wrong.
Oh I didn’t know that, that’s cool, I’ll give it a whirl! Thanks for sharing.
Oh man, thanks for this, I didn’t know that there was a still-live form of Atom and I’ll have to check this out.