
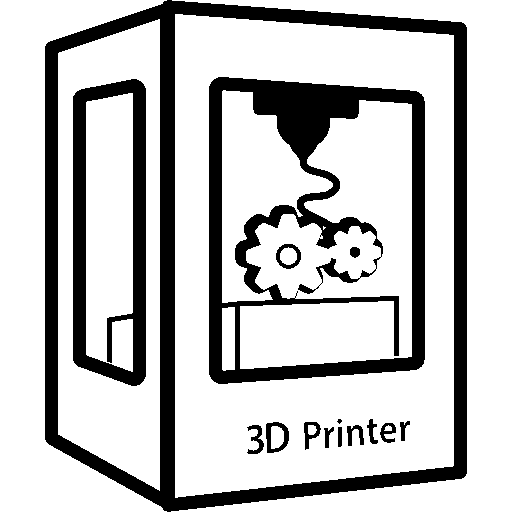
I don’t know about this particular model, but the brand is well liked for their higher end printers. At budget price points there’s only so far you can stretch the BOM cost so I don’t know how much more I would expect of this printer vs other budget entries.
You’re four forks deep now Slic3r to Prusa Slicer to Bamboo’s slicer to Orca. It also borrowed a lot of ideas from Super Slicer. Since it’s open source, and has been gaining some momentum, it seems to have a decent amount of contributors
Why Orca?