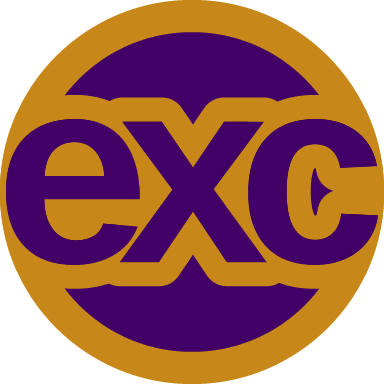
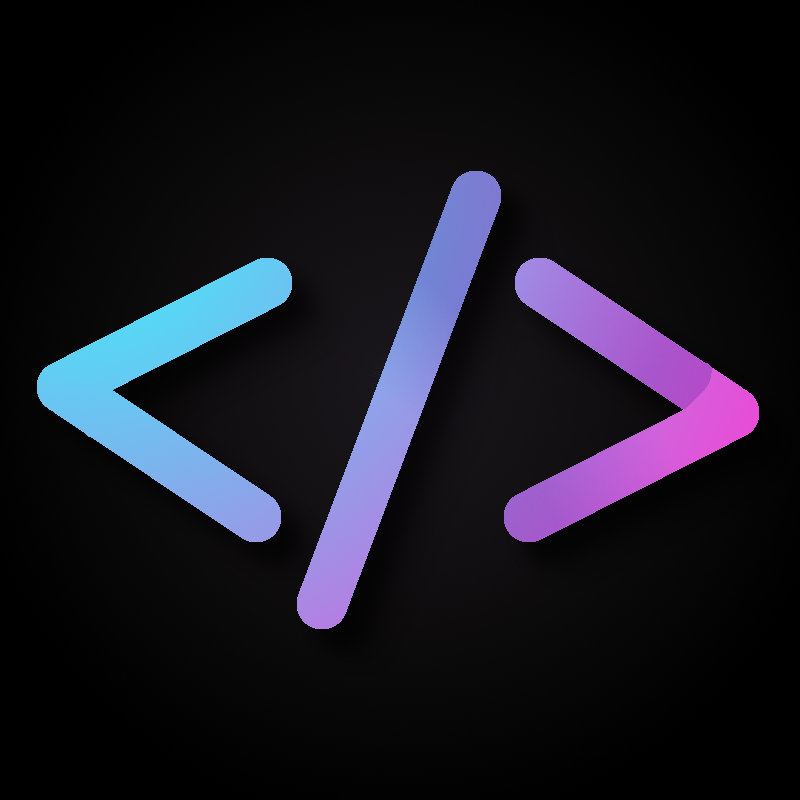
I remember seeing a lot about activeX controls as a kid but not understanding them much. As an adult reading this I was like “were they a way to run arbitrary code on a user’s computer?”
Yes, they were a way to run arbitrary code on a user’s computer.
And electronics hobbyists!