
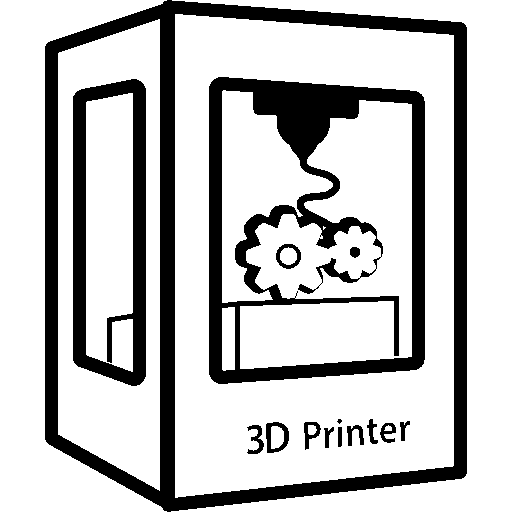
I disagree with all your points. What kind of servos are you talking about?
BLDC and AC servos maintain full torque at stop too, and have about 2-3× the torque of a stepper of similar size.
The only way a stepper can rival a servo for precision is with a high degree of microstepping, which is far from guaranteed positioning with open loop control.
I haven’t directly compared response time between steppers and servos, but I would be extremely surprised if there’s a significant enough difference to worry about. Most servo-controlled machines are larger and so are designed to accelerate slower than a printer, if that’s what you mean. This is intentional because inertia is a thing you have to worry about, not because the servo reacts to command changes slowly.
There are valid reasons steppers are used on printers, but it’s not because they have superior performance.
This guy gets it. Thanks for the excellent post.