
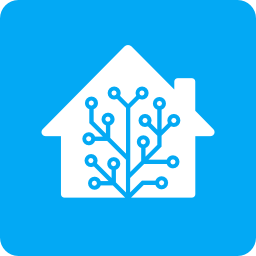
Bluetooth or wifi, depending on the number of accesspoints…
Anyway, a really smart hack!
Bluetooth or wifi, depending on the number of accesspoints…
Anyway, a really smart hack!
Sony SRS-RA8000 owner here. Can confirm it works with the plugin mentioned above.
Using Harman Kardon hardware yields in a way less happy experience.
Ok, this is really over the topz but I like it. Wouldn’t be too hard, to open the gate when the mower engages.
Clever and nice touch of adding the drain.
First check the dontvacuum.me site for compatibility.
Flash with modified firmware, run valetudo and disconnect from the Chinese cloud.
Valetudo integrates with HA.
The Husqvarna/Gardena etc. are pretty much all one design with different colors.
Checkout https://www.robonect-shop.de/ this is an add on for those devices and unlocks nice features.
Mqtt, pushover, weather etc.etc.
Definitely recommended.
Edit: the HA integration: https://github.com/geertmeersman/robonect
Depending on the size, but I’ve had success with super glue and baking soda.
https://www.instructables.com/Baking-Soda-Reinforcing-Glue-Repair/
Openscad, just because…
https://www.printables.com/model/73924-esp32-devkit-v4-case-openscad
Probably convenient to have access to an 3D printer
Ender 3v2 as starter here, doubled the price with a lot of upgrades/modifications. Got it running rock solid with Klipper and a microswiss direct drive.
Grabbed the piggy bank and am now really satisfied with my voron 2.4.
But very pleased with the fact I started with the Ender and got to learn then basics.
As far as I can suggest anything; start with something with a large installed base, so it will be easy to find answers or (hardware) solutions to your problems. I can tell you, the installed base for Ender is large, but the quality of the hardware, is what you pay. And they are cheap…
I use OpenSCAD to have a declarative method to ‘design’ boxes for my electronic projects. So boxes and lids with hinges and stuff.
When I need something with accurate measurements but a more complex design, FreeCad is the go-to tool. Sprockets, PS5 controller loading-station, bolts and nuts.
Blender probably can be used too, but I have never used it.
If the printer runs a Marlin variation as firmware (Ender probably does), you can run octoprint on a Raspberry pi or more powerful stuff. Running in docker should be doable, you just need to route the serial-usb connection into the container running ocotoprint. Klipper user with Mainsail on a RPI4 here, no experience with a dockerized octoprint.
The most slicers have some calibration prints to tune flow/temperature etc. Do them before starting that 9 hour print job…
Designing stuff: FreeCad and OpenSCAD. Lots of YouTube material for educational purposes.
Regarding the printer, this depends on the make/model/manufacturer, but the more serious people (not starting a flame war here, just my observation) tend to use Klipper. Most printers run some form of Marlin, but most can run Klipper as an alternative firmware.
And there are the slicers… A huge amount of choice here, but one way or the other, most are forks/spinoffs of previous work. Personal choice here is SuperSlicer, mostly due to its interface and me being too lazy to use OrcaSlicer of one of the other options.
But beware: tuning, measuring adjusting will take a lot of time. And the entire 3d printing community likes is.
And that probably won’t be the end.
Very happy (and after 2 years usage still extremely unskilled) with FreeCad.
Oh boy this sucks… I’m running a ender 3v2 with a pi4 and created a custom USB cable without the 5V connected, just to be on the save side.
Creality should really do a better job…
This is nice! When in need, this can be a life saver. Thank you!
Recently switched from Marlin to Klipper. It looks like there is a sample configuration for your N32 board. Maybe a good custom firmware for your printer…
To flatten the learning curve, I’ve installed the Mainsailos image on a raspberry pi 4 and followed a lot of documentation / YT to get things up and running. The results are great, still got to get input shaping and the resonance measurements, but quite a difference!
I’m using a bl-touch. So the firmware will need to know the delta between the tip of the probe and your extruder (the z-offset).
I doubt creating a mesh without a probe is possible. At the moment I use a mesh with 9*9 points. This gets saved to eeprom and (see the other comment) loaded at startup using a g-code. I let it do a three-point probe after hearing the bed, so the software knows if it needs to tilt the mesh.
I do use octoprint, but these capabilities are all embedded in the software by mriscoc.
I own an Ender and installed alternative firmware (mriscoc professional firmware) which gives me a feature to probe the bed on multiple points and store this mesh in memory.
Now the firmware ‘knows’ about all the holes and hills on the bed and compensates for it.
You want to look for terms like bed mesh leveling, when you’ve got a probe attached, this technique can really help.
Holidays are coming, maybe I can find some time to give it another go. Last attempts was 20mm/sec, but maybe it needs even less speed.
If everything else fails, I’ll reach out here. Thanks.
Yes, this is really soft material. Got the printer to produce some results, but a lot of blobs between gaps. Never achieved nice gaps between edges.
Tried this but my result is nearly as good.
Blowtorch will heat this up way too hot.
Try to get it to a high enough temperature to insert filament to do a cold pull and repeat…
Electrical heat gun (paint stripper) is hot enough. Gas based torches will change the stiffness of your material and you will regret it.